PROTIG 201 AC/DC is a professional TIG welding solution for welding all metal types up to 4 mm thick (steel, stainless steel, aluminium, copper and titanium). It ensures a very high level of precision in many areas such as production, maintenance or pipe work.
SIX AC/DC TIG PROCESSES
- Welding current: 10 – 200 A (AC TIG), 10 – 160 A (DC TIG)
- Standard DC TIG: Ensures high-quality welding on all ferrous materials, such as steel, stainless steel as well as copper, its alloys and titanium, etc.
- Pulsed DC TIG: Controls the melting temperature, limits deformation and allows sheet metal from 0.3 mm thick to be assembled effectively.
- Spot DC TIG: Pre-assemble ferrous metals by spot welding them together.
- Easy AC TIG: Makes using the welding machine even easier thanks to predefined user settings. The operator only has to select the tungsten electrode’s diameter on the machine’s control panel.
- Standard AC TIG: Designed for welding aluminium and its alloys (Al, AlSi, AlMg and AlMn, etc.). An alternating current effectively cleans the aluminium for perfect welds.
- Spot AC TIG: Pre-assemble aluminium parts and accessories by spot welding them together.
TWO COATED-ELECTRODE WELDING MODES
- Welding current: From 10 – 160 A (MMA)
- Standard MMA: Uses basic and rutile electrodes up to Ø 4 mm.
- Pulsed MMA: Makes it easier to weld in a vertical-upright position (nozzles/pipelines).
DESIGNED FOR USER COMFORT
- Two ignition types: HF (without contact) or ARC-LIFT (with contact) for electro-sensitive environments.
- Three trigger management modes:
– 2T: Maintains pressure on the trigger throughout the welding process.
– 4T: To start welding, press the trigger once and then press the trigger again to stop the welding process.
– 4T «LOG»: The operator can switch between two separate welding currents by quickly pressing the trigger (hot and cold current).
- MMA welding aids:
– Anti-Stick: Reduces the risks of the electrode sticking to the workpiece if it comes into contact with it.
– Hot Start: Assists in igniting the arc and can be adjusted according to the type of metal being welded.
– Arc Force: This fully adjustable feature regulates the arc length deviations.
- VRD (Voltage Reduction Device): the welding current is only delivered when the electrode is in contact with the workpiece (not originally activated).
ROBUST DESIGN FOR ALL ENVIRONMENTS
- Equipped with a reinforced chassis and anti-shock protections
- Compact and lightweight design
- Current/Voltage displayed after welding (DMOS/QMOS)
- Stores up to 50 welding programs per process
- Remote control connections
HIGH-TECH POWER SUPPLY
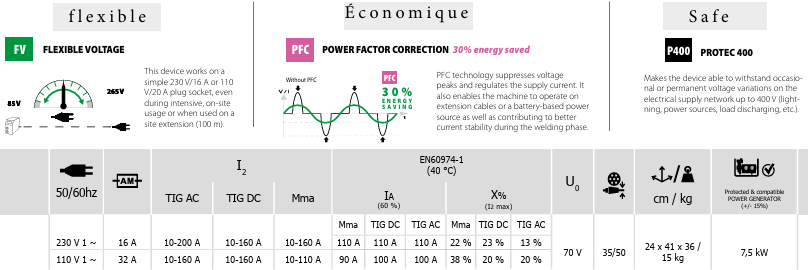
Download Catalogue